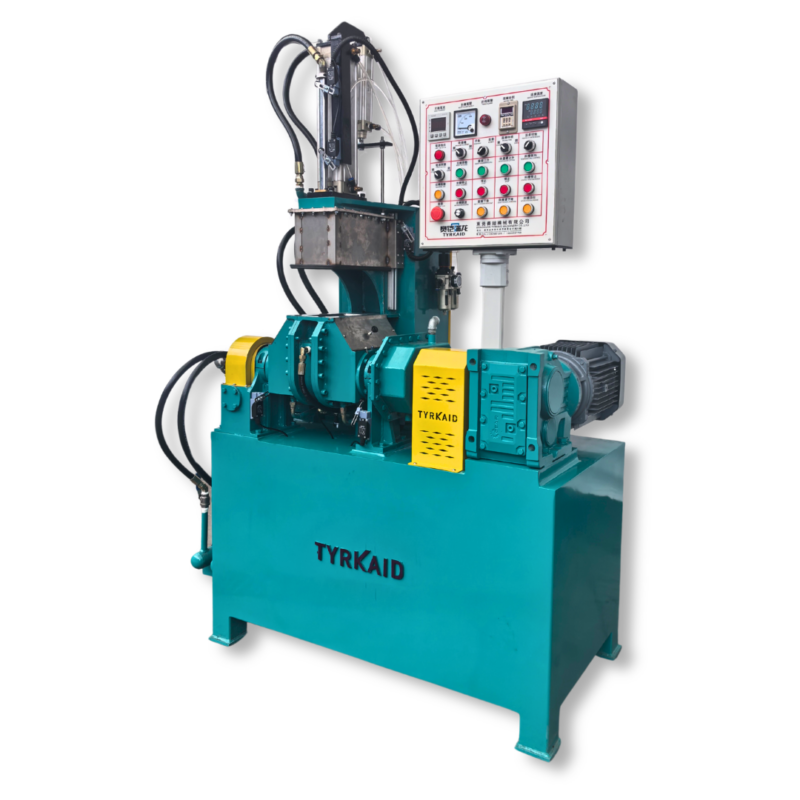
In the fast-paced world of manufacturing, efficiency is key. For industries that rely on rubber and plastic compounds, such as tire manufacturing, automotive parts production, and consumer goods, the ability to produce high-quality materials quickly and consistently is crucial. This is where internal mixers, also known as Banbury mixers, come into play. These powerful machines have revolutionized the mixing process, enabling manufacturers to complete large-scale rubber and plastic mixing in a fraction of the time compared to traditional methods. In this article, we will explore how internal mixers significantly enhance productivity, their working principles, and the benefits they bring to modern manufacturing.
1. The Need for Speed in Rubber and Plastic Mixing
Rubber and plastic mixing is a critical step in the production of a wide range of products, from tires and seals to hoses and consumer goods. Traditionally, this process was carried out using open mills, which, while effective, were time-consuming and labor-intensive. As demand for rubber and plastic products grew, manufacturers needed a solution that could handle larger volumes of material while maintaining consistent quality.
Enter the internal mixer. Invented by Fernley H. Banbury in 1916, this machine was designed to mix rubber and plastic compounds more efficiently than ever before. By combining high-speed rotors, precise temperature control, and advanced mixing technology, internal mixers have become the go-to equipment for manufacturers looking to boost productivity.
2. How Internal Mixers Work: The Science Behind the Speed
At the heart of an internal mixer is its mixing chamber, which houses two rotors that rotate in opposite directions. These rotors are equipped with wings or blades that create a shearing action, breaking down the rubber or plastic and dispersing additives evenly throughout the compound. The process begins with the loading of raw materials into the chamber, followed by the application of heat and mechanical shear to soften the material and blend the additives.
One of the key features that enable internal mixers to work so quickly is their high-speed rotors. These rotors can operate at speeds of up to 60 rpm, depending on the model, allowing for rapid mixing of large batches of material. Additionally, modern internal mixers are equipped with advanced cooling systems that prevent overheating, ensuring that the mixing process can continue uninterrupted.
The result is a homogeneous mixture that is ready for further processing in a matter of minutes, compared to the hours it might take using traditional methods.
3. The Productivity Advantage of Internal Mixers
The ability of internal mixers to complete large-scale mixing in a short time offers several productivity advantages:
- Faster Production Cycles: By reducing the time required for mixing, internal mixers enable manufacturers to complete production cycles more quickly. This is particularly important in industries like tire manufacturing, where high volumes of material are needed on a tight schedule.
- Higher Output: Internal mixers can handle larger batches of material compared to open mills, allowing manufacturers to produce more in less time. This increased output can help meet growing demand and improve profitability.
- Consistent Quality: The precise control over temperature, rotor speed, and mixing time ensures that each batch of material is uniform in quality. This consistency reduces the need for rework and minimizes waste.
- Reduced Labor Costs: The automated nature of internal mixers reduces the need for manual labor, allowing manufacturers to allocate resources more efficiently.
4. Real-World Applications: Where Speed Matters
Internal mixers are used in a wide range of industries where speed and efficiency are critical. Some notable applications include:
- Tire Manufacturing: In the tire industry, internal mixers are used to compound rubber with additives like carbon black and sulfur. The ability to produce large volumes of high-quality rubber quickly is essential for meeting the demands of the automotive market.
- Automotive Parts: Internal mixers are used to produce rubber seals, gaskets, and hoses for vehicles. The fast mixing process ensures that these components can be manufactured in large quantities without compromising on quality.
- Consumer Goods: From shoe soles to rubber gloves, internal mixers play a key role in the production of everyday items. The speed and efficiency of these machines help manufacturers keep up with consumer demand.
- Industrial Products: Internal mixers are also used to produce industrial rubber products, such as conveyor belts and seals. The ability to mix large batches of material quickly is crucial for industries that rely on these products for their operations.
5. The Future of Internal Mixers: Even Faster and Smarter
As technology continues to advance, internal mixers are becoming even more efficient and intelligent. Some of the trends shaping the future of these machines include:
- Automation and AI: The integration of automation and artificial intelligence (AI) is enabling internal mixers to optimize the mixing process in real-time. This not only increases speed but also improves the quality of the final product.
- Energy Efficiency: Manufacturers are increasingly focused on reducing energy consumption. Modern internal mixers are being designed with energy-efficient motors and cooling systems to minimize their environmental impact.
- Advanced Materials: As new materials are developed, internal mixers are being adapted to handle them. This includes bio-based rubbers and biodegradable plastics, which are becoming more popular in response to environmental concerns.
- Digitalization: The use of IoT (Internet of Things) sensors and data analytics is allowing manufacturers to monitor and optimize the performance of their internal mixers. This digital transformation is helping to further boost productivity and reduce downtime.
6. Conclusion
Internal mixers have transformed the rubber and plastic industries by enabling manufacturers to complete large-scale mixing quickly and efficiently. Their ability to handle high volumes of material, maintain consistent quality, and reduce production costs has made them an indispensable tool for modern manufacturing.
As technology continues to evolve, internal mixers will become even faster, smarter, and more versatile, helping manufacturers meet the growing demands of the global market. Whether it’s producing tires for vehicles, rubber seals for industrial equipment, or consumer goods, internal mixers will remain at the forefront of the manufacturing process, driving productivity and innovation.