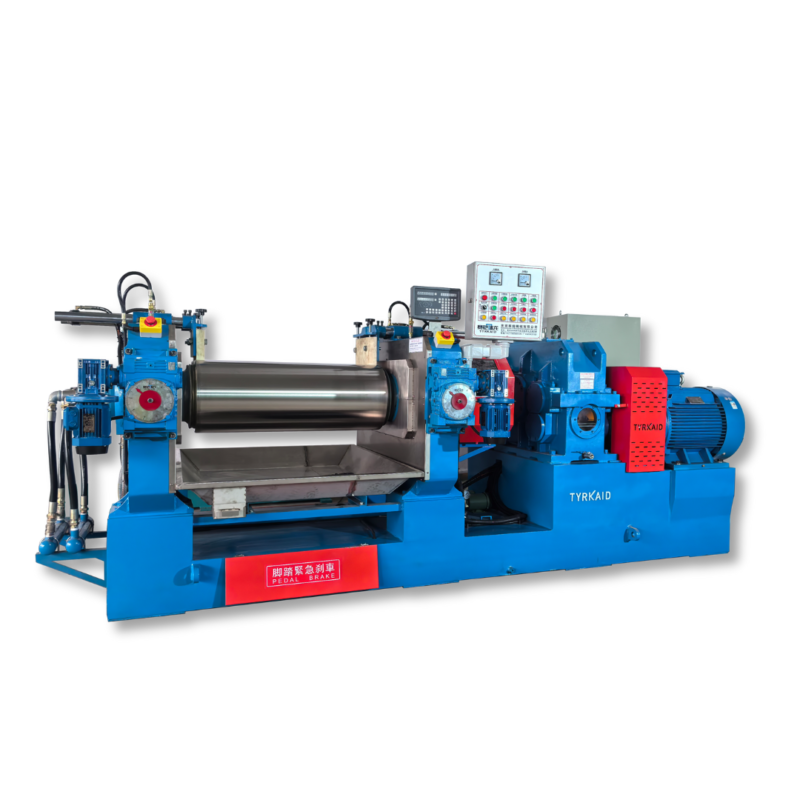
Introduction
The rubber industry has long been a cornerstone of economic development in Southeast Asia, contributing significantly to the region’s GDP, employment, and export revenues. Countries such as Thailand, Indonesia, Malaysia, Vietnam, and the Philippines are among the world’s largest producers and exporters of natural rubber. The industry’s growth has been driven by a combination of favorable climatic conditions, abundant natural resources, and a strategic geographical location that facilitates global trade. However, the rubber industry’s evolution has not been solely dependent on natural advantages; technological advancements have played a crucial role in shaping its trajectory. Among these technologies, open mill machines, also known as two-roll mills, have been instrumental in transforming rubber processing and manufacturing.
This article provides a comprehensive analysis of the impact of open mill machines on the development of the rubber industry in Southeast Asia. It explores the historical context of rubber production in the region, the technological evolution of open mill machines, their applications in rubber processing, and their influence on productivity, quality, and sustainability. Additionally, the article examines the challenges and opportunities associated with the adoption of open mill machines and their implications for the future of the rubber industry in Southeast Asia.
Historical Context of Rubber Production in Southeast Asia
The Rise of Rubber Plantations
The rubber industry in Southeast Asia has its roots in the late 19th and early 20th centuries when rubber plantations were established to meet the growing global demand for natural rubber. The region’s tropical climate, with its high rainfall and consistent temperatures, proved ideal for rubber tree cultivation. The introduction of Hevea brasiliensis, the rubber tree species native to the Amazon rainforest, marked the beginning of large-scale rubber production in Southeast Asia.
By the early 20th century, countries such as Malaysia, Indonesia, and Thailand had emerged as major rubber producers. The establishment of rubber plantations was often accompanied by the development of infrastructure, including roads, railways, and ports, to facilitate the transportation of rubber products to global markets. The rubber industry became a key driver of economic growth, providing employment opportunities for millions of people and generating significant export revenues.
The Role of Technology in Rubber Processing
As the rubber industry expanded, so did the need for efficient and reliable processing technologies. Early rubber processing methods were labor-intensive and time-consuming, relying on manual techniques to extract latex from rubber trees and process it into usable forms. The introduction of machinery, such as open mill machines, revolutionized rubber processing by automating and streamlining key production processes.
Open mill machines, which consist of two rotating rollers that mix and refine rubber compounds, became a staple in rubber factories across Southeast Asia. These machines enabled manufacturers to produce high-quality rubber products with greater consistency and efficiency, paving the way for the region’s dominance in the global rubber market.
Technological Evolution of Open Mill Machines
Early Developments
The concept of the open mill machine dates back to the early 19th century when the first two-roll mills were developed for mixing and refining rubber compounds. These early machines were relatively simple in design, consisting of two horizontally aligned rollers made of cast iron or steel. The rollers were heated to facilitate the mixing process, and the gap between them could be adjusted to control the thickness of the rubber sheet.
Despite their simplicity, early open mill machines represented a significant advancement in rubber processing technology. They allowed manufacturers to achieve a more uniform distribution of additives, such as sulfur, carbon black, and accelerators, within the rubber compound. This uniformity was critical for producing rubber products with consistent properties, such as elasticity, tensile strength, and durability.
Modern Innovations
Over the years, open mill machines have undergone significant technological advancements to meet the evolving needs of the rubber industry. Modern open mill machines are equipped with advanced features that enhance their performance, efficiency, and safety. Some of the key innovations include:
- Automated Control Systems: Modern open mill machines are often equipped with computerized control systems that allow operators to precisely adjust parameters such as roller speed, temperature, and gap width. These systems improve the accuracy and repeatability of the mixing process, reducing the risk of human error and ensuring consistent product quality.
- Energy-Efficient Designs: Energy consumption has become a major concern for rubber manufacturers, particularly in regions where energy costs are high. Modern open mill machines are designed to minimize energy consumption through the use of high-efficiency motors, variable frequency drives, and optimized roller designs. These energy-efficient features not only reduce operating costs but also contribute to the industry’s sustainability goals.
- Enhanced Safety Features: Safety is a top priority in rubber processing, given the potential hazards associated with operating heavy machinery. Modern open mill machines are equipped with safety features such as emergency stop buttons, protective guards, and automated shut-off mechanisms to prevent accidents and protect workers.
- Versatility: Modern open mill machines are designed to handle a wide range of rubber compounds, including natural rubber, synthetic rubber, and rubber blends. They can also process various additives and fillers, making them suitable for producing a diverse array of rubber products, from tires and industrial seals to footwear and consumer goods.
Applications of Open Mill Machines in Rubber Processing
Mixing and Compounding
One of the primary applications of open mill machines in the rubber industry is mixing and compounding. The process involves blending raw rubber with various additives to create a homogeneous rubber compound with specific properties. The additives may include vulcanizing agents, accelerators, fillers, plasticizers, and anti-degradants, each of which plays a crucial role in determining the final characteristics of the rubber product.
Open mill machines are particularly well-suited for mixing and compounding due to their ability to apply shear forces to the rubber compound. As the rubber passes through the gap between the rollers, it is subjected to intense mechanical action, which disperses the additives evenly throughout the material. This ensures that the rubber compound has consistent properties, such as elasticity, hardness, and resistance to wear and tear.
Mastication
Mastication is another important application of open mill machines in rubber processing. This process involves mechanically breaking down the long polymer chains in raw rubber to reduce its viscosity and improve its processability. Mastication is particularly important for natural rubber, which has a high molecular weight and can be difficult to process in its raw form.
Open mill machines are highly effective for mastication because they can apply controlled shear forces to the rubber, breaking down the polymer chains without degrading the material. The process also generates heat, which further softens the rubber and makes it easier to work with. Once the rubber has been masticated, it can be more easily mixed with additives and shaped into the desired form.
Sheet Formation
Open mill machines are also used to produce rubber sheets of uniform thickness and quality. The process involves passing the rubber compound through the rollers, which compress and flatten the material into a thin sheet. The thickness of the sheet can be controlled by adjusting the gap between the rollers, allowing manufacturers to produce sheets of varying thicknesses for different applications.
Rubber sheets produced using open mill machines are widely used in the manufacture of a variety of products, including conveyor belts, gaskets, seals, and flooring materials. The uniform thickness and consistent quality of the sheets ensure that the final products meet the required specifications and performance standards.
Calendering
Calendering is a process that involves passing rubber through a series of rollers to produce thin, continuous sheets or films. While calendering is typically performed using specialized calendering machines, open mill machines can also be used for small-scale calendering operations. The process is particularly important for producing rubber sheets and films used in the manufacture of tires, automotive components, and consumer goods.
Open mill machines used for calendering are equipped with precision rollers that can produce sheets and films with tight tolerances and smooth surfaces. The process also allows for the incorporation of reinforcing materials, such as fabric or metal mesh, into the rubber sheet, enhancing its strength and durability.
Impact of Open Mill Machines on the Rubber Industry in Southeast Asia
Increased Productivity and Efficiency
The adoption of open mill machines has had a profound impact on the productivity and efficiency of the rubber industry in Southeast Asia. By automating and streamlining key processing steps, open mill machines have enabled manufacturers to produce rubber products more quickly and with greater consistency. This has allowed the region’s rubber industry to meet the growing global demand for rubber products, particularly in sectors such as automotive, construction, and consumer goods.
The increased productivity and efficiency brought about by open mill machines have also contributed to the competitiveness of Southeast Asia’s rubber industry on the global stage. By reducing production costs and improving product quality, manufacturers in the region have been able to offer high-quality rubber products at competitive prices, attracting buyers from around the world.
Improved Product Quality
Open mill machines have played a crucial role in improving the quality of rubber products produced in Southeast Asia. The ability to achieve a uniform distribution of additives and fillers within the rubber compound ensures that the final products have consistent properties, such as elasticity, tensile strength, and resistance to wear and tear. This consistency is critical for meeting the stringent quality standards required by industries such as automotive, aerospace, and healthcare.
In addition to improving the consistency of rubber products, open mill machines have also enabled manufacturers to produce rubber compounds with enhanced properties. For example, the precise control of processing parameters, such as temperature and shear rate, allows manufacturers to optimize the vulcanization process, resulting in rubber products with superior strength, durability, and resistance to aging.
Sustainability and Environmental Impact
The rubber industry in Southeast Asia has faced increasing pressure to adopt more sustainable practices in recent years, driven by growing environmental concerns and stricter regulations. Open mill machines have played a key role in helping the industry meet these challenges by reducing energy consumption, minimizing waste, and improving resource efficiency.
Modern open mill machines are designed to be more energy-efficient, with features such as high-efficiency motors and variable frequency drives that reduce power consumption. This not only lowers operating costs but also reduces the industry’s carbon footprint. Additionally, the precise control of processing parameters enabled by open mill machines helps to minimize material waste, as manufacturers can produce rubber products with tighter tolerances and fewer defects.
Furthermore, open mill machines have facilitated the use of sustainable materials in rubber processing. For example, manufacturers can use open mill machines to process bio-based rubbers and recycled rubber materials, reducing the industry’s reliance on non-renewable resources and contributing to a more circular economy.
Employment and Skill Development
The adoption of open mill machines in the rubber industry has also had a significant impact on employment and skill development in Southeast Asia. While the automation of rubber processing has reduced the need for manual labor in some areas, it has also created new opportunities for skilled workers who can operate and maintain advanced machinery.
The use of open mill machines requires a workforce with specialized knowledge and skills in areas such as machine operation, process control, and quality assurance. This has led to the development of training programs and vocational education initiatives aimed at equipping workers with the skills needed to succeed in the modern rubber industry. As a result, the adoption of open mill machines has contributed to the upskilling of the workforce and the creation of higher-paying, more stable jobs in the region.
Challenges and Opportunities
Despite the many benefits of open mill machines, their adoption in the rubber industry in Southeast Asia has not been without challenges. One of the primary challenges is the high initial cost of acquiring and installing advanced open mill machines. For small and medium-sized enterprises (SMEs) in the region, the capital investment required to purchase modern machinery can be a significant barrier to entry.
Another challenge is the need for ongoing maintenance and technical support to ensure the reliable operation of open mill machines. This requires access to skilled technicians and spare parts, which can be difficult for manufacturers in remote or underdeveloped areas. Additionally, the rapid pace of technological advancement means that manufacturers must continually invest in upgrading their equipment to remain competitive.
However, these challenges also present opportunities for innovation and collaboration. For example, governments and industry associations in Southeast Asia can play a key role in supporting SMEs by providing financial incentives, technical assistance, and access to training programs. Additionally, partnerships between manufacturers and technology providers can facilitate the development of more affordable and user-friendly open mill machines tailored to the needs of the region’s rubber industry.
Future Trends and Implications
Digitalization and Industry 4.0
The rubber industry in Southeast Asia is poised to benefit from the ongoing digitalization of manufacturing processes, often referred to as Industry 4.0. Open mill machines are increasingly being integrated into digital ecosystems that leverage technologies such as the Internet of Things (IoT), artificial intelligence (AI), and big data analytics to optimize production processes and improve decision-making.
For example, IoT-enabled open mill machines can collect and transmit real-time data on key processing parameters, such as temperature, pressure, and roller speed. This data can be analyzed using AI algorithms to identify patterns and trends, enabling manufacturers to optimize their processes and reduce waste. Additionally, predictive maintenance systems can use data from open mill machines to anticipate equipment failures and schedule maintenance before issues arise, minimizing downtime and reducing repair costs.
Sustainable Manufacturing
As the global demand for sustainable products continues to grow, the rubber industry in Southeast Asia will need to adopt more environmentally friendly practices. Open mill machines will play a crucial role in this transition by enabling the use of sustainable materials, reducing energy consumption, and minimizing waste.
For example, manufacturers can use open mill machines to process bio-based rubbers derived from renewable resources, such as guayule and dandelion rubber. These materials offer a more sustainable alternative to traditional petroleum-based synthetic rubbers and can help reduce the industry’s environmental impact. Additionally, open mill machines can be used to recycle and reprocess waste rubber materials, contributing to a more circular economy.
Customization and Flexibility
The increasing demand for customized rubber products is driving the need for more flexible and adaptable manufacturing processes. Open mill machines are well-suited to meet this demand, as they can be easily adjusted to produce rubber compounds with specific properties and characteristics.
For example, manufacturers can use open mill machines to produce rubber compounds tailored to the unique requirements of different industries, such as automotive, aerospace, and healthcare. This flexibility allows manufacturers to offer a wider range of products and services, enhancing their competitiveness in the global market.
Regional Collaboration and Integration
The rubber industry in Southeast Asia is highly interconnected, with countries such as Thailand, Indonesia, and Malaysia playing key roles in the global supply chain. As the industry continues to evolve, there will be opportunities for greater regional collaboration and integration, particularly in areas such as technology transfer, research and development, and market access.
For example, regional partnerships can facilitate the sharing of best practices and technical knowledge, enabling manufacturers to adopt the latest advancements in open mill machine technology. Additionally, collaborative research initiatives can drive innovation in areas such as sustainable materials, energy-efficient processing, and digitalization, further enhancing the region’s competitiveness in the global rubber market.
Conclusion
Open mill machines have had a transformative impact on the rubber industry in Southeast Asia, driving improvements in productivity, quality, and sustainability. By automating and streamlining key processing steps, open mill machines have enabled manufacturers to produce high-quality rubber products more efficiently and at a lower cost. This has contributed to the region’s dominance in the global rubber market and supported economic growth and development.
However, the adoption of open mill machines has also presented challenges, particularly for small and medium-sized enterprises that may struggle with the high initial costs and technical complexities of advanced machinery. Addressing these challenges will require a collaborative effort involving governments, industry associations, and technology providers to ensure that the benefits of open mill machines are accessible to all players in the industry.
Looking ahead, the rubber industry in Southeast Asia is poised to benefit from ongoing technological advancements, particularly in areas such as digitalization, sustainable manufacturing, and customization. By embracing these trends and continuing to invest in innovation, the region’s rubber industry can maintain its competitive edge and contribute to a more sustainable and prosperous future.