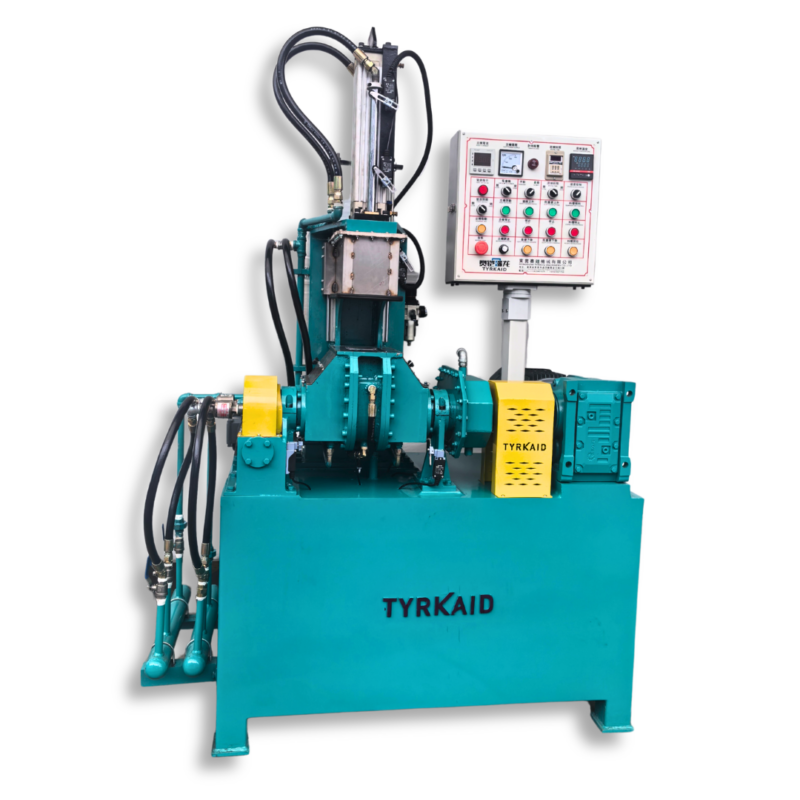
Mixing mills, also known as internal mixers or Banbury mixers, are essential equipment in the rubber and plastic industries. These machines are designed to mix raw materials, such as rubber compounds, plastics, and additives, to create homogeneous mixtures that are crucial for manufacturing high-quality products. This article explores the importance of mixing mills, their working principles, key components, and their applications in modern industries.
1. Introduction to Mixing Mills
Mixing mills are heavy-duty machines used to blend various raw materials into a uniform mixture. They are widely used in the rubber industry for compounding rubber with additives like carbon black, sulfur, and oils. In the plastic industry, they are used to mix polymers with fillers, stabilizers, and colorants. The primary goal of a mixing mill is to ensure that all components are evenly distributed, which is critical for achieving consistent product quality.
The invention of the mixing mill revolutionized the rubber and plastic industries by replacing manual mixing processes with automated, efficient, and precise machinery. Today, mixing mills are indispensable in industries that require high-volume production of rubber and plastic products, such as tire manufacturing, automotive parts, and consumer goods.
2. Working Principles of Mixing Mills
Mixing mills operate on the principle of shear mixing. The machine consists of a mixing chamber with two rotors that rotate in opposite directions. The rotors have blades or wings that create a shearing action, which breaks down the raw materials and blends them into a homogeneous mixture.
The process begins with the loading of raw materials into the mixing chamber. As the rotors rotate, the materials are subjected to intense mechanical shear and heat, which softens the rubber or plastic and allows the additives to disperse evenly. The temperature and pressure inside the chamber are carefully controlled to ensure optimal mixing conditions.
Once the mixing process is complete, the mixture is discharged from the chamber and can be further processed, such as by calendering or extrusion, to create the final product.
3. Key Components of a Mixing Mill
A typical mixing mill consists of several key components that work together to achieve efficient and consistent mixing:
- Mixing Chamber: The chamber is where the raw materials are loaded and mixed. It is designed to withstand high temperatures and pressures.
- Rotors: The rotors are the heart of the mixing mill. They rotate in opposite directions to create the shearing action needed for mixing.
- Drive System: The drive system, usually powered by an electric motor, provides the energy needed to rotate the rotors.
- Cooling System: Mixing generates heat, so a cooling system is essential to maintain the temperature within the desired range.
- Control Panel: Modern mixing mills are equipped with advanced control panels that allow operators to monitor and adjust parameters such as temperature, rotor speed, and mixing time.
- Discharge Door: Once mixing is complete, the mixture is discharged through a door at the bottom of the chamber.
4. Applications of Mixing Mills
Mixing mills are used in a wide range of industries, including:
- Tire Manufacturing: In the tire industry, mixing mills are used to compound rubber with additives to create the tread, sidewalls, and other components of tires.
- Automotive Parts: Mixing mills are used to produce rubber and plastic parts for vehicles, such as seals, gaskets, and hoses.
- Consumer Goods: Many everyday products, such as shoe soles, rubber gloves, and plastic containers, are made using materials processed in mixing mills.
- Industrial Products: Mixing mills are also used to produce industrial rubber products, such as conveyor belts, hoses, and seals.
5. Advantages of Modern Mixing Mills
Modern mixing mills offer several advantages over traditional mixing methods:
- Efficiency: Mixing mills can process large volumes of material in a short time, making them ideal for high-volume production.
- Consistency: The automated nature of mixing mills ensures that each batch of material is mixed to the same high standard.
- Flexibility: Mixing mills can handle a wide range of materials and formulations, making them versatile tools for manufacturers.
- Energy Efficiency: Advanced cooling systems and energy-efficient motors reduce the energy consumption of modern mixing mills.
- Precision Control: With advanced control panels, operators can precisely control the mixing process to achieve the desired results.
6. Challenges and Future Trends
Despite their many advantages, mixing mills face some challenges. One of the main challenges is the wear and tear of the rotors and mixing chamber due to the high mechanical stress and abrasive nature of some materials. Regular maintenance is required to ensure the longevity of the equipment.
Another challenge is the need to adapt to new materials and formulations. As the rubber and plastic industries evolve, mixing mills must be able to handle new types of raw materials and additives.
Looking to the future, several trends are likely to shape the development of mixing mills:
- Automation: The integration of automation and artificial intelligence (AI) will enable even greater precision and efficiency in the mixing process.
- Sustainability: There is a growing demand for energy-efficient and environmentally friendly mixing mills that reduce waste and energy consumption.
- Advanced Materials: As new materials are developed, mixing mills will need to be adapted to handle these materials effectively.
- Digitalization: The use of digital tools, such as IoT (Internet of Things) sensors, will allow manufacturers to monitor and optimize the mixing process in real-time.
7. Conclusion
Mixing mills play a vital role in the rubber and plastic industries, enabling the production of high-quality materials that are essential for a wide range of products. With their ability to efficiently and consistently mix raw materials, mixing mills have become indispensable tools for manufacturers.
As technology continues to advance, mixing mills will become even more efficient, precise, and versatile, helping manufacturers meet the growing demands of the modern world. Whether it’s producing tires for vehicles, rubber seals for industrial equipment, or plastic containers for consumer goods, mixing mills will remain at the heart of the manufacturing process.
This article provides a comprehensive overview of mixing mills, their importance, and their future in the rubber and plastic industries. If you need further details or adjustments, feel free to ask!